Developing a commercial dash-cam solution
One of our first customers, Matrix Telematics needed a simple but effective method of ensuring the wiring on the back of their commercial dashcams couldn’t be removed by the vehicle driver. We worked with the customer to refine their idea into a 3D model which could be printed at scale, minimise material usage and ultimately ensure the part was as cost effective as possible without affecting performance.
Volumes were initially low as we prototyped the design, and having completed the trials we now supply both the manufacturer and their network of re-sellers with stock on-demand.
Why did it make sense to use 3D printing?
Simply put:
- Injection mould tooling is new designs is too expensive – With camera models changing frequently and the potential of needing to adjust and refine the design, injection moulding is not cost effective.
- With 3d printing there’s no need to hold large stocks – orders of up to 200 pieces can be printed and shipped the same day.
- Camera models change frequently – New designs can be introduced as soon as they are finished resulting in greater flexibility and shorter time to market
- Stock can be delivered quickly – With our current facility we can print 1000 of these brackets in 3 hours allowing super fast turnaround of orders.
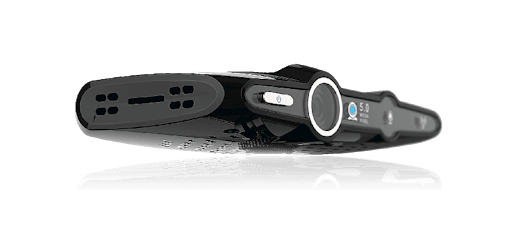